The plants can be designed once and then shipped anywhere in the world
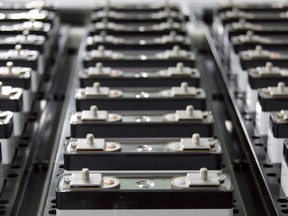
Article content
The ongoing debate about how to reduce the cost of batteries has some advocating for the use of new metals or experimenting with different chemicals, while others say a local supply chain is all that’s needed.
Dan Blondal, chief executive of Burnaby-based Nano One Materials Corp., sees a different path: “cookie-cutter” battery plants.
That is, he thinks the best way to beef up North America’s battery supply chain is to make the plants so generic that they can be designed once and then shipped anywhere in the world.
Advertisement 2
Article content
“There’s not enough engineers in the world to build out all this capacity in custom plants,” he said.
To that end, his company recently struck a partnership with Vancouver-based Worley Chemetics, with Nano One bringing its intellectual property on how to produce active cathode materials with less waste and byproducts and Worley bringing its expertise on fabricating the equipment needed to actually produce the battery cathodes.
Together, the two companies plan to produce the equipment for Nano One’s “one-pot” cathode process at Worley’s recently expanded alloy fabrication shop in Pickering, Ont., and then license it to other battery companies. They haven’t disclosed the exact details of how such commercial arrangements will work yet, in part because they haven’t yet received any orders.
There’s not enough engineers in the world to build out all this capacity in custom plants
Dan Blondal
“We found the relationship to be almost an uncannily good fit,” Andrew Barr, president of Worley Chemetics, said.
Barr, Laura Leonard, group president of Technology Solutions at Worley Ltd., the Australian engineering company that’s a parent company to Chemetics — which already has business ties with chemical companies in the battery space — and Blondal all convened at Pickering on Thursday for the official opening of the plant’s expansion.
Advertisement 3
Article content
At nearly 100,000 square feet, the plant is decked out with plasma arc welders, laser-cutting machines and other specialized fabrication machines.
The only issue is that the two companies haven’t received any orders yet.
For now, Barr said the plant will make small- and medium-sized reactors for the nuclear energy sector, which he joked is seeing “explosive” growth.
Leonard said the partnership is aimed at taking the energy transition goals from “ambition to reality,” and part of that is what she called the “standardization” of equipment, so you design something once and then build it repeatedly.
“Nano One has described it as ‘design one, build many,’” she said. “We talk about it as the standardization that’s needed in order to have those capital projects deployed faster and at the pace and scale to reach net zero by 2050.”
Of course, even big battery factory projects’ proponents will still need to obtain permits, hookups to the electrical grid and to consult with local communities.
But Blondal said the key is building a plant that will actually work, and both Nano One and Worley Chemetics understand how to work with the corrosive acids needed to build batteries.
Advertisement 4
Article content
It’s a new business strategy for Nano One, which in 2019 had been working to develop business opportunities in China. By 2021, it had shifted its focus to North America and the West.
In 2022, it purchased an 80,000-square-foot lithium-iron phosphate battery production plant in Candiac, Que., which it is using to prove out its technology and to continue innovating.
Recommended from Editorial
For Worley Chemetics, it’s also a shift into a new line of business.
“They’ve designed hundreds of plants in the oil and gas sector and now they want to do it in the battery sector,” Blondal said.
• Email: gfriedman@postmedia.com
Bookmark our website and support our journalism: Don’t miss the business news you need to know — add financialpost.com to your bookmarks and sign up for our newsletters here.
Article content